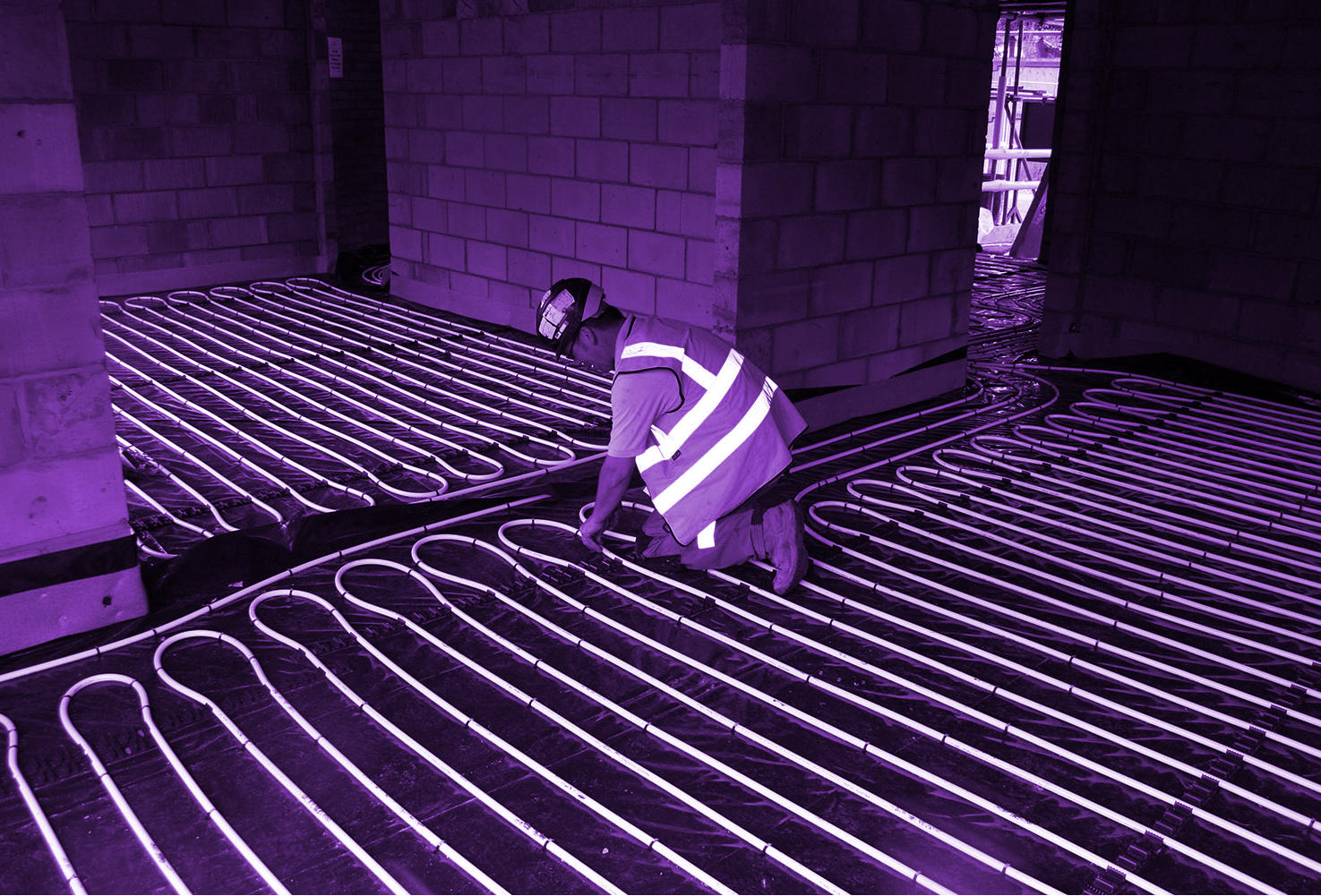
Concrete Slab with Underfloor Heating: The Smart Way to Build Warm, Efficient Floors
As suspended timber ground floors become less popular amongst new build construction firms. Block and beam and insulated concrete slab are becoming the staple. When insulation is a priority, a slab is the optimum and is easily paired with underfloor heating (UFH)
Concrete Slab or Suspended Floor? Choosing the Right Foundation for UFH
Recently, a client approached Resolve regarding the replacement of his suspended ground floor with a concrete slab.
Personally, I am an advocate for suspended floors, primarily because I consider upgrading or retrofitting them to be a more sustainable and DIY-friendly option. With a little guidance, many people can implement a suspended floor retrofit themselves, making it a viable option for those who might otherwise be unable to afford the upgrade. I believe that the opportunity to enhance your home is more valuable than forgoing an improvement simply due to budget constraints.
That said, there are certain benefits to slab construction, particularly given the specifics of each project. These benefits may include more and/or better thermally preforming insulation, greater resilience to moisture beneath the structure, and increased durability, which can provide peace of mind. In some cases, a concrete slab also offers the potential to introduce thermal mass into your property, which could be advantageous depending on your home’s location usage and heating system.
There are two principal methods for laying a concrete slab, both of which I have outlined below. While the dimensions of the build-up may vary slightly, the general principles remain the same. I have also expanded the discussion on typical practices and provided a more refined specification for each.
Additionally, I have a third option that, under the right conditions, would be more advantageous than both standard methods. You can discover why by reading on. For the purpose of this discussion all three cases incorporate under floor heating, as this is the most efficient low temperature heating method, as we transition away from fossil fuel heating to electric heating with heat pumps.
What Is a Warm Slab and Why Builders Love It
Quite literally, this method insulates the concrete slab, resulting in a slab that is warmed along with the house. This additional thermal mass inside the property helps regulate temperature fluctuations. When combined with low-temperature underfloor heating (UFH), it provides an efficient and stable indoor temperature. The downside is that there is a significant warm-up period, during which the slab must be heated before the rooms begin to feel the effects of the heating.
In this case, the most efficient practice would involve heating the slab once per heating season. Depending on the temperature difference, this could take up to 24 hours to warm up for the first time each season. In theory, this means that during the time you are away from your home during the day and the heating system is off, the residual heat in the slab will keep the house warm. When the heating system is turned back on in the afternoon, only a small amount of energy will be needed to bring the house back up to the ideal living temperature.
The UFH, powered by a heat pump, would run for extended periods throughout the heating season, but a good weather compensation system is crucial to prevent overheating and reduce energy waste. This is particularly relevant to low energy house. UFH is generally not suited for PassiveHouse, they have extremely small heating demands and would overheat.
Common practise might see a 150mm (polyisocyanurate) PIR insulation under a 150mm slab, with the UFH situated in a screen layer on top of the concrete. This is shown to the right. This large volume of concrete would require over 100 times the energy to heat than the air in the room it sits below.
The slab could be more cost effective and responsive to heating if the slab could be slimmed as much as possible. The National House Building council (NHBC) Standards only accept ground-supported floor slabs with at least 100 mm thick concrete. Or 100mm including a monolithic screed. As shown in the diagram 1. This would be 50 times the energy to heat the slab than the air in the room above.
The compressive strength of a residential ground floor can be met comfortably with 100mm of concrete, provided that appropriate measures are taken to prevent cracking. Additionally, the need for a screed layer could be avoided if the underfloor heating (UFH) were laid directly within the slab.
This approach would require a confident UFH installer who is prepared to pour the slab themselves, rather than relying on a traditional concrete contractor. One option is to fix the UFH to the reinforcement bar. Attempting to optimise the slab in this way may prove challenging when engaging tradespeople, as it involves asking them to depart from their usual, tried-and-tested methods. However, a general contractor may have greater influence over their employees and subcontractors, which could make it easier to accommodate such specific requirements.
Whilst the aggregate below buffers moisture in the ground the insulation in a warm slab is close to contact with the ground and potentially a moist environment. I would also recommend using extruded polystyrene insulation (XPS) close to the DPM instead of PIR for its better moisture resistance, compressive strength and durability.
A Cold Slab and Warm House
Yes, you’ve guessed correctly. In this case, the insulation is placed above the concrete slab, meaning the slab remains relatively cold compared to the internal temperature of the house. The main benefit of this arrangement is that all the heat from the underfloor heating (UFH) is directed into the room, warming the air quickly. This setup is particularly well suited to occupancy patterns where the house is vacant for extended periods. Such as weekends.
Typically, the UFH is installed within a screed layer, which does provide some thermal mass benefits. A 50mm screed layer as shown to the right would result in roughly 25 times the energy stored in the screed than the air of the room. However, I find the installation process for this approach to be far from ideal, as it involves two separate curing periods, first for the slab and then again for the screed.
With a screed, the UFH would usually be pinned to the top of the insulation, or installed within a purpose-made insulation layer that features pre-formed grooves for pipework. The preferred dry finish for easy construction would be the UFH in specifically designed structural boards laid over the insulation. Several products are available, this not only helps distribute the load evenly but also provides a suitable surface for installing the final floor finish. These products include a high conductive material to help spread the heat evenly across the floor.
No Slab, No Problem: Innovative UFH Without Traditional Concrete
This design entirely eliminates the need for concrete. An approach aimed at reducing embodied carbon while offering a cost-effective and DIY-friendly solution. It represents a logical evolution beyond simply refurbishing a suspended timber floor and aligns with the growing interest in low-carbon construction alternatives.
In the absence of a concrete slab to distribute structural loads, the performance of the floor relies on a high-strength engineered board, laid over rigid PIR insulation with high compressive strength. The load path continues down through a sand blinding layer and a damp proof membrane (DPM), terminating at a well-compacted aggregate sub-base.
While this approach is unsuitable for floors expected to carry high point loads (for obvious reasons), it broadly follows the same structural principle as the other slabs, which also depend on the insulation layer for load distribution. Like the cold slab, it benefits from low thermal mass and fast warm-up times, making it particularly well suited to properties with intermittent heating schedules. For long-term durability, it would be best practice to specify extruded polystyrene (XPS) insulation immediately above the DPM, given its resistance to moisture and ground pressure.
However, this method is currently best suited to adventurous or experienced self-builders and renovators who are willing to gather additional technical evidence. In this case, certification from a qualified structural engineer is essential and may be required to satisfy both Building Control and insurance underwriters.
It’s important to understand that most UK new build warranty providers, including NHBC and LABC Warranty still expect a concrete slab or timber floor in ground-bearing situations. Any alternative must usually be supported by structural calculations and may require product certification under schemes like BOPAS, NHBC Accepts, or LABC Assured.
From an insurance and mortgage perspective, using a non-concrete ground floor can introduce complications:
- Mortgage lenders often rely on RICS surveys, and unconventional construction methods can trigger red flags or require further investigation.
- Buildings insurers may ask whether the property is of standard construction? answering ‘yes’ when using an unorthodox floor build-up could result in rejected claims if damage occurs later.
- You may be asked whether the floor is concrete or timber? answering neither, means at best additional documentation will be needed to ensure coverage.
For these reasons, anyone pursuing this method should be prepared to retain detailed drawings, specifications, and certification to support future insurance, warranty, or lending requirements.
The Build Up of an Insulated Concrete Floor
In addition to the above industry best practise recommends 150mm of compacted MOT Type 1 as a subbase. Which accommodates the changes in moisture content and spread the loads to the ground. A minimum of 25mm of sand blinding to protects a double layered and taped DPM. It is this which either the concrete or insulation sits on. The DPM must be continuous without tears and join with the damp proof course on the external wall’s damp proof course (DPC) which is a minimum of 150mm above external finish floor.
Any warm slab should have expansion considered into the design. As a bare minimum there should be insulation around the perimeter for the slab to stop thermal bridging to the external wall. But this is also compressible and acts an expansion joint. Residential slabs with a dimension over 6m require an additional expansion joint or crack inducing saw cut.
If reducing embodied carbon is the top priority then you can even consider foamed glass aggregate. It has significantly less CO2 than other petrochemical insulations mentioned above. But does have a higher U-value (unit of heat conductivity). Consequently, it would also replace the use for standard MOT 1 aggregate and sand blinding. Meaning you could use 325mm of the product. This would come at significant cost.
You should of course always carefully read the application recommendations for any product and seek an engineer’s advice. Each project is different and designs should be specifically curated.
Getting the Balance Right: Comfort, Efficiency, and Cost
In the case of the client, there are several expectable solutions, but finding the optimum is depended on the client’s needs and the current situation. The current suspended floor detail provides approximatly 330 mm from the underside of the finished floor to the earth. The client has requested a floor U-value of 0.15 W/m²K or better, and has expressed strong interest in the long-term performance and peace of mind a ground-bearing slab can offer.
With that in mind the no slab solution is not an option. It was recommend the suspended floor was replaced with a 100mm cold slab. The concrete slab and DPM (damp-proof membrane) combine to make a resilient water-resistant base. This allows for the use of highest-performance PIR insulation above the slab, limiting its depth.
Over the PIR, we propose a dual-purpose structural UFH (underfloor heating) board, serving both as the pipe carrier and base. The finished floor (e.g., tile, engineered wood, or dry-laid system) would then be applied directly on top. A screed is also an option for added thermal mass but would increase the thickness of the floor build up by a minimum of 30mm.
This build-up would limit excavating to roughly 125 mm and achieve an overall floor U-value of approximately 0.14 W/m²K, providing excellent thermal performance, faster response times, and a robust floor construction. It should also be well within the means of a standard building contractor.
Insulation Meets Innovation: Your Ideal Floor Build-Up Starts Here
Undergoing this amount of work is not something to be taken lightly. Resolve Sustainability understands that any intervention should be considered within the context of a whole-house retrofit plan for the most effective energy and cost-saving impact. By using modelling technology, a comprehensive picture can be created to strategically target the most cost-beneficial changes.
Do not hesitate to contact Resolve, where no project is too small or too big, and we believe that every homeowner deserves access to the expertise needed to make home improvements that benefit both wider society and the individual.